Fasteners for applications with high requirements
The electric drive components in EVs, such as the engine, battery and power electronics, pose special challenges to the fasteners and functional components like valves. As a result, the fasteners and functional components for the technical aspects of the electric vehicle powertrain are very important. The best way to respond to the challenges that arise when developing these components, such as electrical insulation, compact design, light weight and resistance to corrosion, is provided by innovative fastener solutions. These also add value through ergonomic or automated assembly. ITW delivers components that meet these tough requirements.
Multifunctional components
The most important applications for fasteners in electric vehicle powertrains are the battery, the high-voltage routing, and the mechanical drivetrain with transmission and engine. Functional components like valves also play a decisive role. Degassing valves ensure the airflow in the event of a thermal runaway, and pressure compensation valves maintain safe operation in many applications. They are waterproof but ensure the pressure compensation with the environment. Emergency drainage valves drain any unwanted water penetration immediately. By acting in combination, these valves prevent overpressure and short circuits.
EV battery components
Degassing Valve:
The degassing valve is an important functional component for venting the battery housing. In the event of a thermal runaway, it enables safe and precise degassing, while also guaranteeing watertightness under normal operation up to IPX6K/9K. The valve is triggered once an adjustable differential pressure is reached. It is available in low-profile designs and with a bayonet interface. Customer adjusted designs are also available to meet individual requirements. In the case of low pressure peaks, the valve closes again and is once again watertight.
Balance Valve:
The balance valve plays an important role in compensating pressure differences in watertight housings with free air space. It uses a adjusted membrane that forms a water barrier while allowing an defined airflow. The ITW team designed this valve to be both cost efficient and compact. It can also compensate high sheet thickness tolerances and ensures watertightness up to IPX6K/9K.
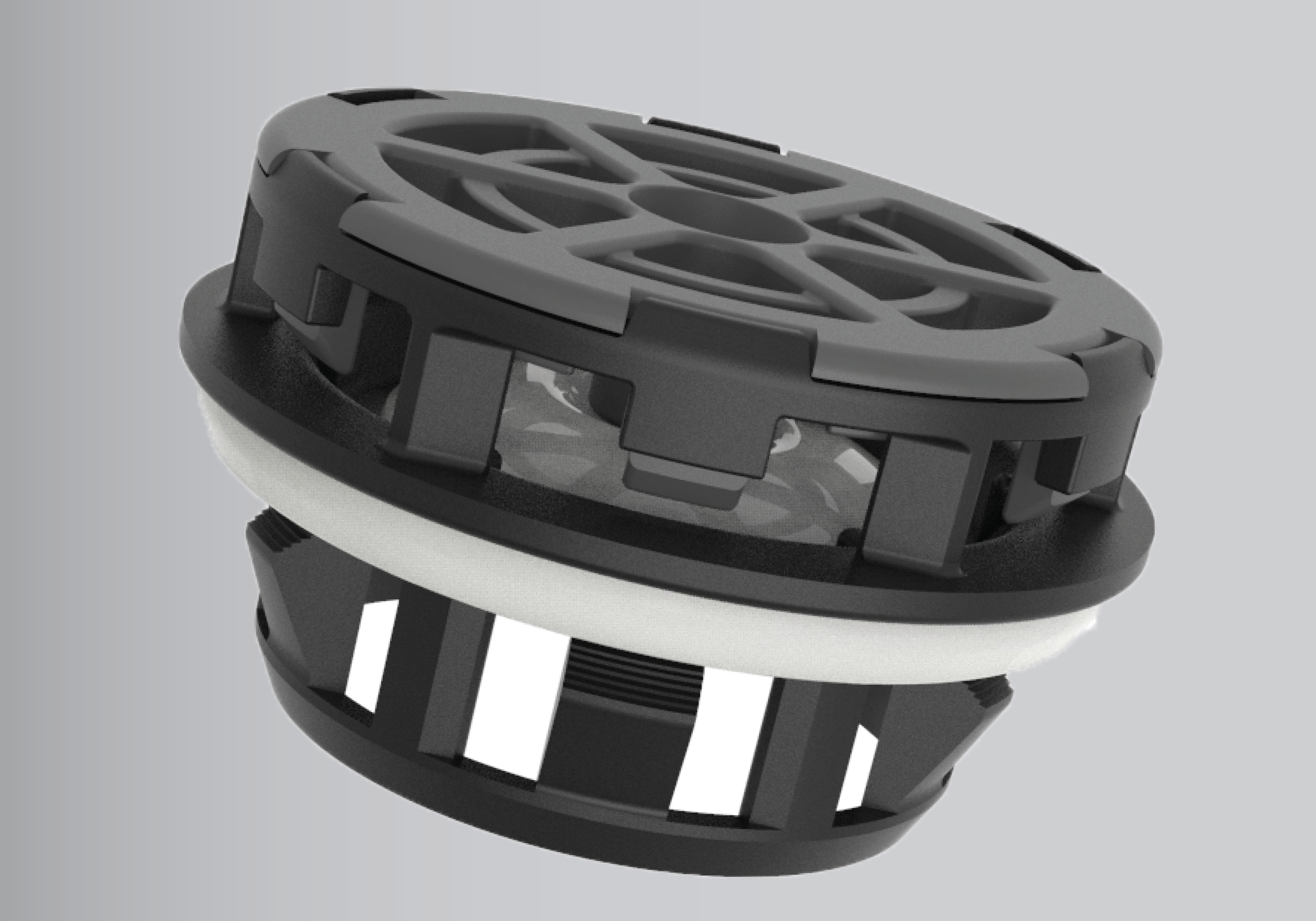
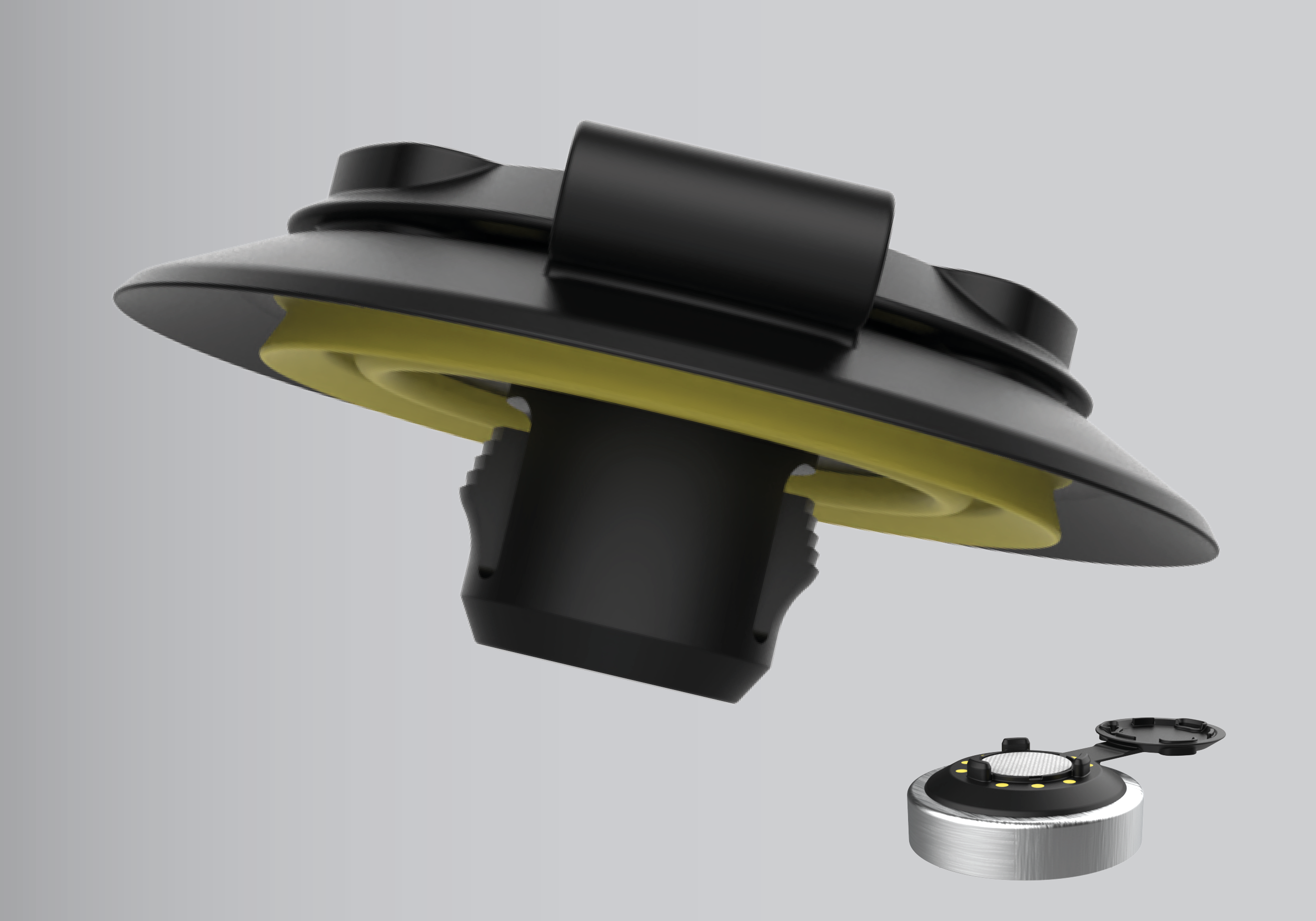
Busbar Fixation:
The ITW team has developed a busbar fixation with a special fastening system that securely connects the high-voltage cables. This busbar system features a cover with a secure fastener that is assembled according to the poka-yoke principle. It secures the component correctly before it can be finally screwed into place. The system also features tolerance compensation and electrical insulation for the high-voltage cable.
Battery Module Fixation:
The ITW EV battery module fixation creates a secure connection and improves the noise, vibration and harshness properties (NVH). The fixation holds the various modules inside the battery pack together, and connects them to form a stiff module. The special ITW design uses molded material to ensure a secure fixation and prevent NVH-related problems.
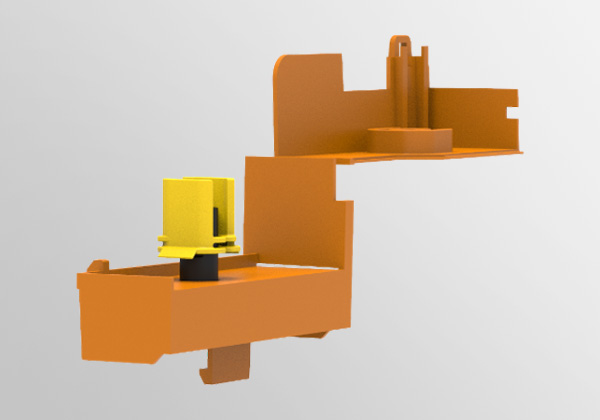
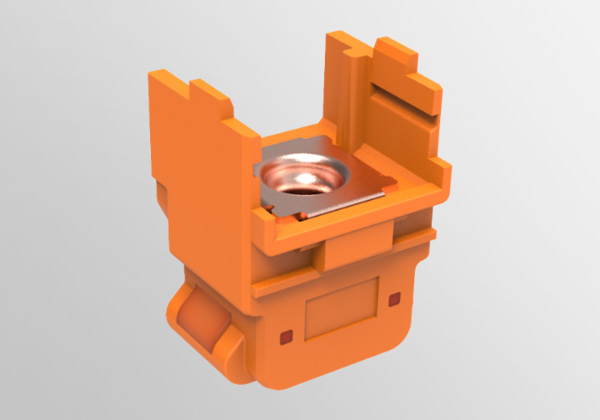
Transmissions and motors
Blind Hole Fastener:
The blind hole fastener is a simple solution for securing NVH damping material and sound covers. It is attached axially to drilled or cast holes. It delivers high holding forces of ≥ 200 N and is incredibly easy to assemble. Thanks to its special design, the blind hole fastener can be removed with a simple rotating motion before being used again. Its modular construction makes the NVH blind hole fastener suitable for various applications.
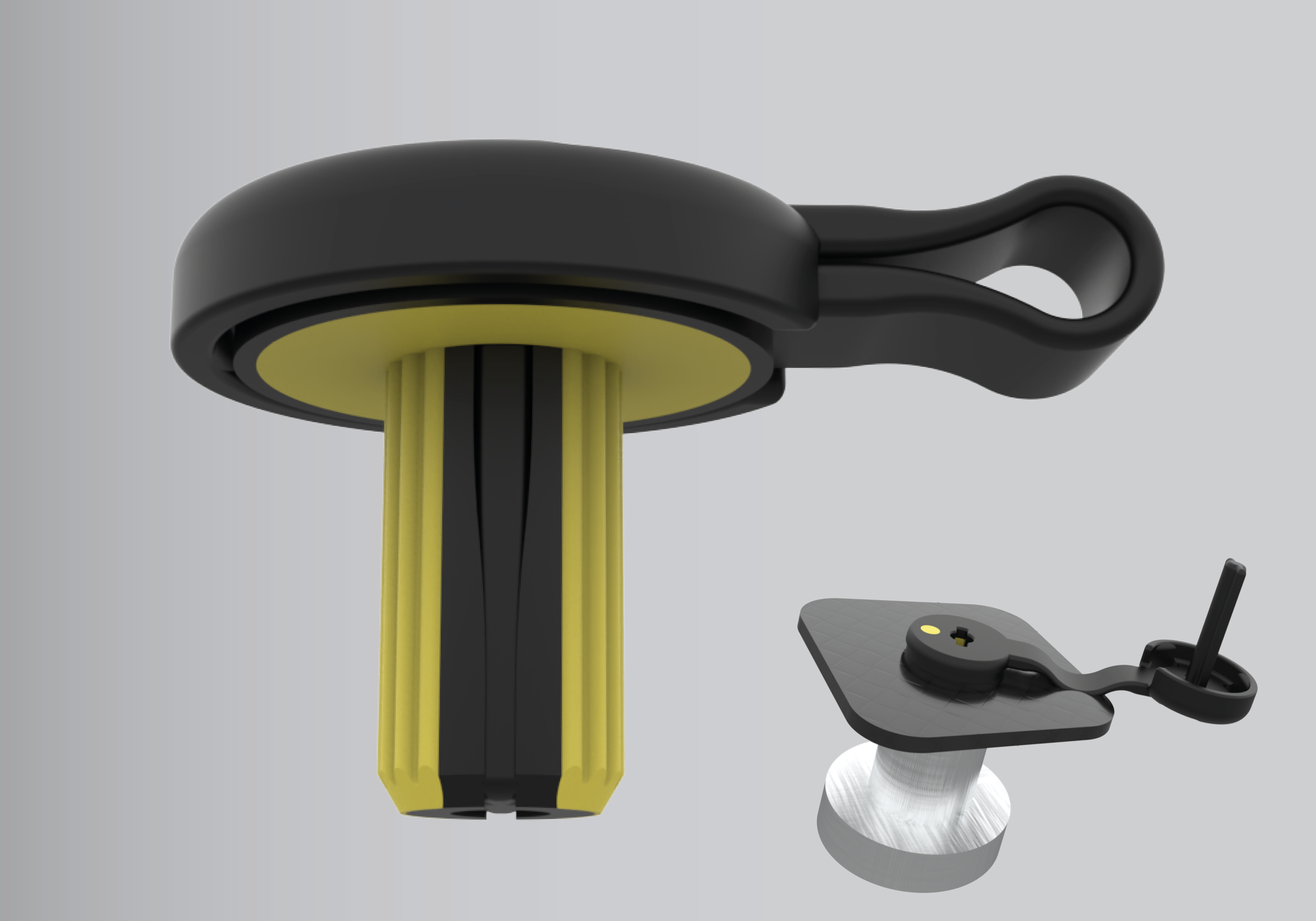
High voltage and cable
Cable Channel High-Voltage:
The cable channel for high-voltage cables is an all-in-one solution for a range of pipes and cables. The integrated inserts, made of metal and/or plastic and TPE, shorten assembly times and can both improve aspects like noise emissions and provide a secure connection in the overall assembly. ITW’s expertise makes it possible to deliver this complete and integrated solution directly to our customers.
Support Brackets:
The support brackets provide a secure connection and support for cables of various different shapes and sizes. They offer cost-efficient advantages in terms of weight reduction, noise damping and reliable cable routing. They are designed according to modern FE methods for bionic design optimization. Their robustness ensures both excellent performance and secure cable fastening.
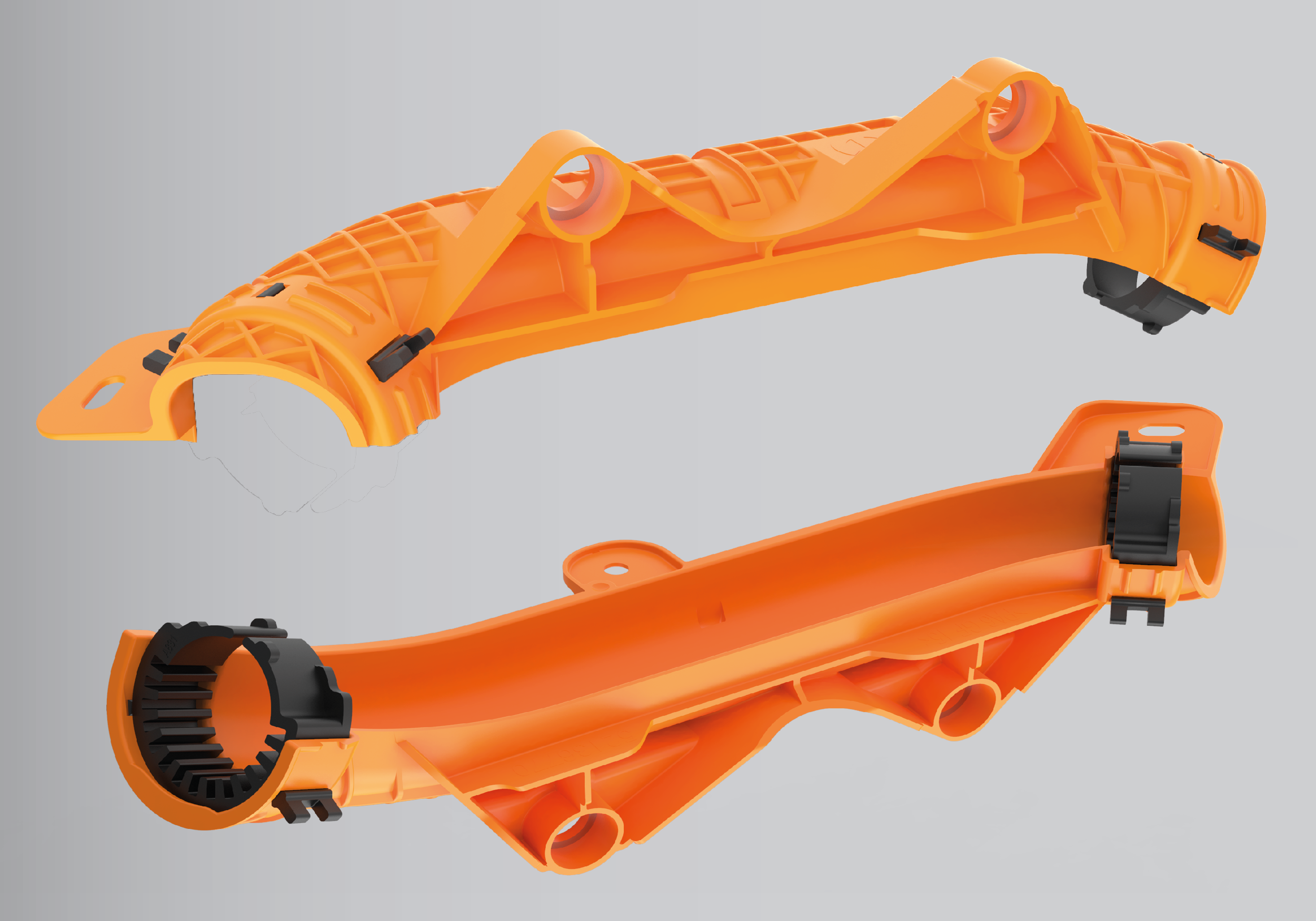
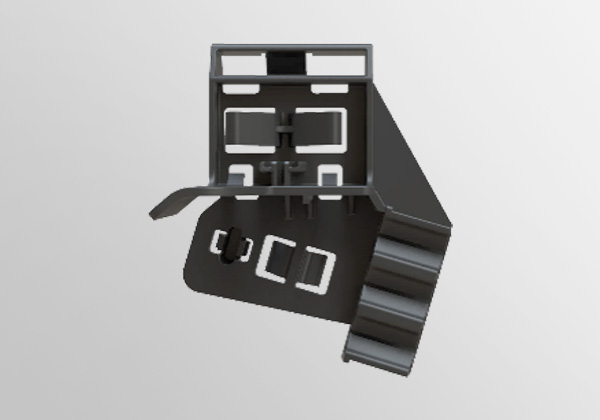
Spring Stem:
The spring stems from ITW were developed specifically for easy assembly in plastic modules. The spring element is designed to absorb the tolerance chains of the components. It also guarantees reliable pre-tension across the service life, even when the components are subject to thermal expansion and lateral contraction.
Shoulder Bolt Fastener:
The shoulder bolt fastener is easy to assemble in plastic elements. Its functional design features a large contact surface that significantly reduces the surface pressure required. As a result, this fastener can also be used in lightweight materials. The shoulder bolt fastener’s reliable hold and stability makes it the ideal solution for secure connections in plastic components.
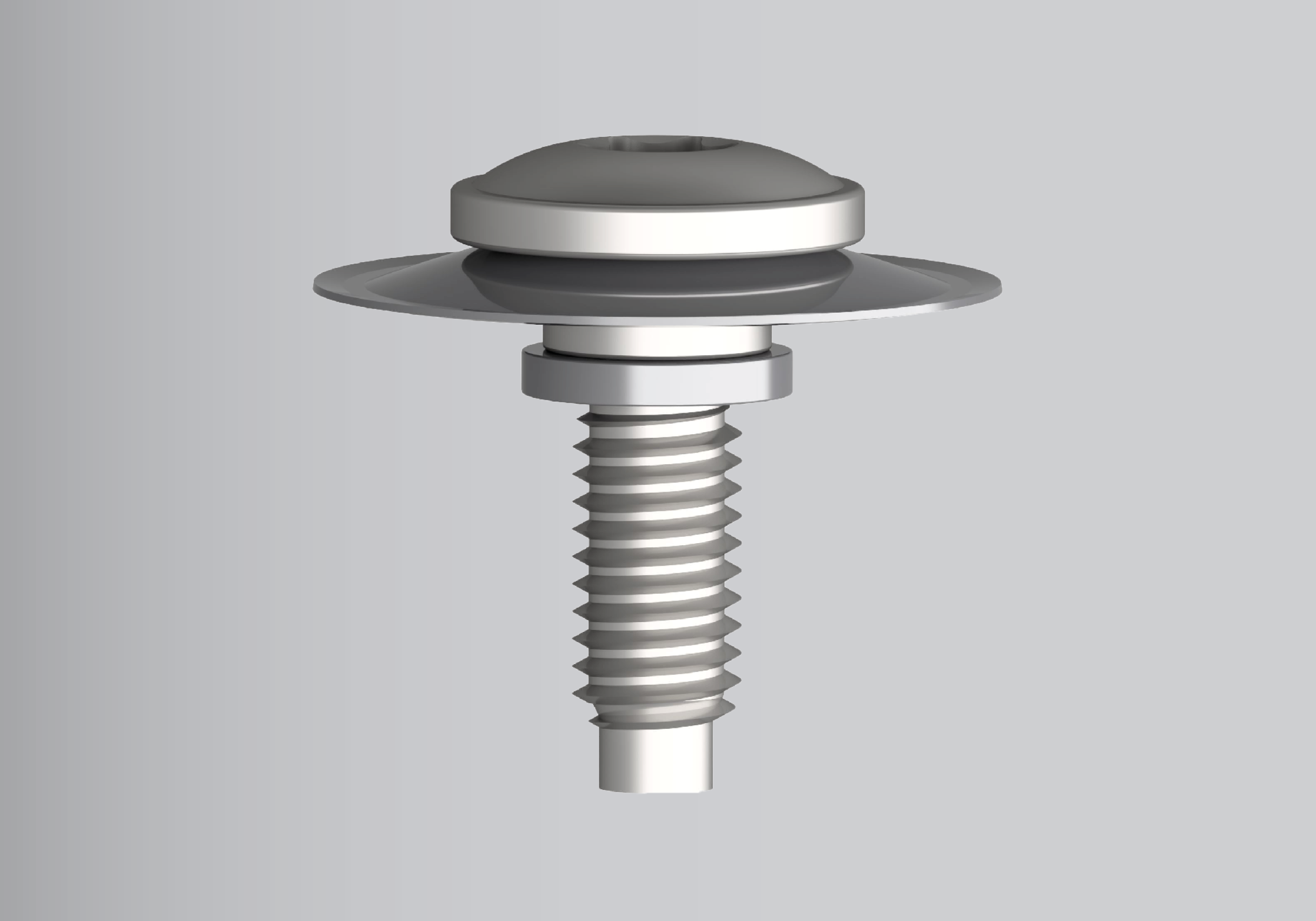
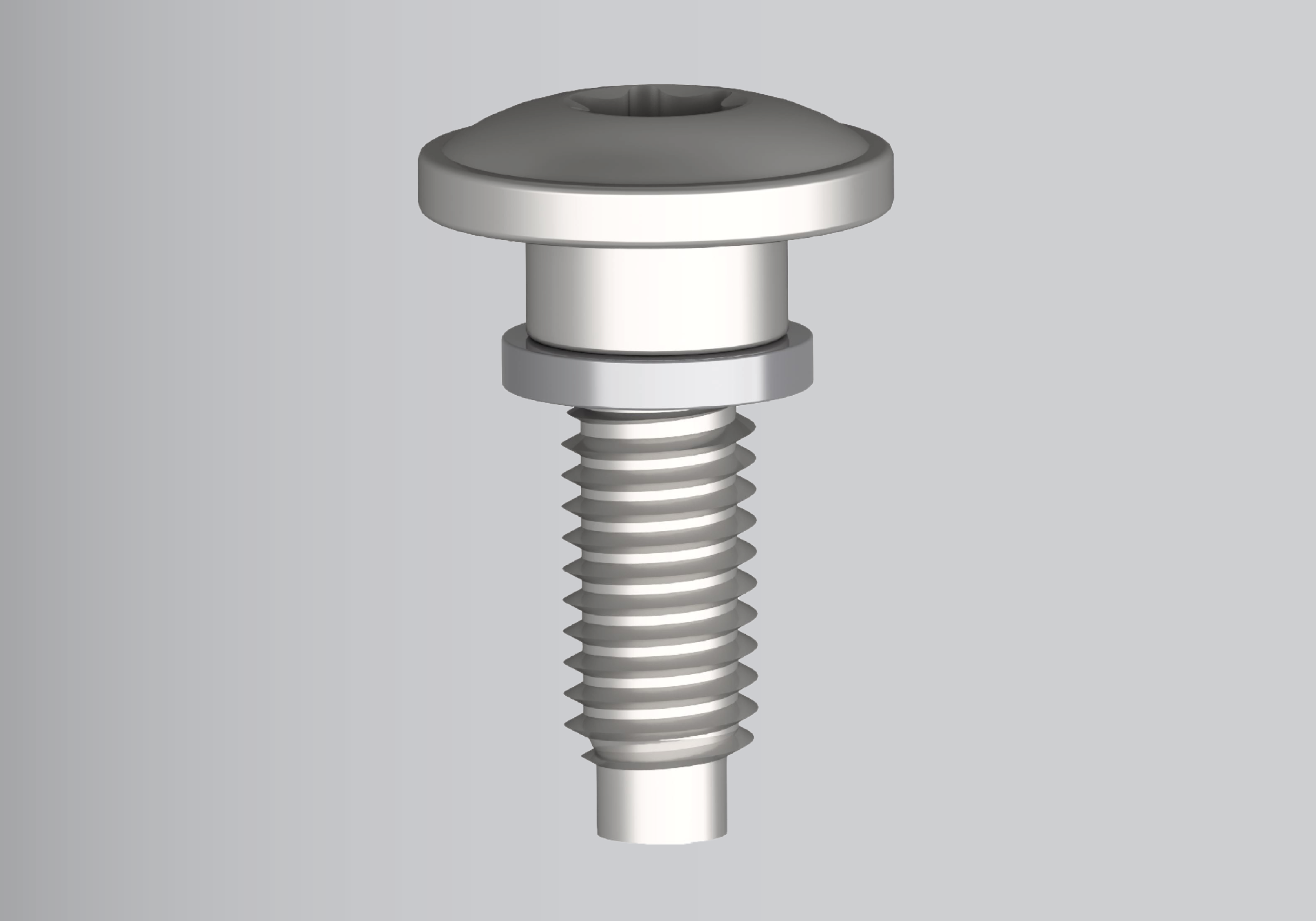
Innovations from ITW Global Fasteners
The drainage valve – the airbag for directly cooled electronics
Innovations from ITW Global Fasteners ensure safety and longevity in electric vehicles. One of these innovations is the drainage valve, developed to improve sustainability.
-
Suitable for cooled batteries or high-power electronics
-
Triggered in the event of a leak in the coolant lines
-
Complete water protection up to IPX9 possible in normal operation
-
Fluid drained away upon reaching a critical level
-
Not sensitive to humidity and changes in climate
The drainage valve is the safe and reliable solution for internal cooling of batteries and high-voltage components. It acts as a kind of airbag for the electronics, preventing short-circuits in high-voltage components caused by unwanted leaks of water or coolant. This valve simplifies the sealing of the cooling system and is an important safety mechanism that stops leaks causing damage.
You are currently viewing a placeholder content from YouTube. To access the actual content, click the button below. Please note that doing so will share data with third-party providers.
More Information